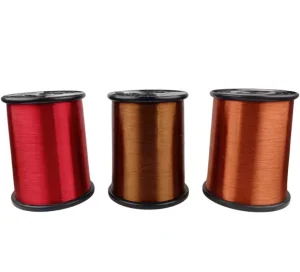
Introduction
Transformer Winding Copper Wire in Electrical Engineering
Transformer winding copper wire is a fundamental component in the field of electrical engineering, crucial for the optimal performance of transformers. The wire’s exceptional electrical conductivity and thermal properties make it an ideal material for winding coils within transformers. These coils are essential for the efficient transfer of electrical energy between circuits, ensuring minimal energy loss and maximum efficiency.
Overview of the Article's Focus on Benefits and Best Practices
This article emphasizes the benefits of using high-quality copper wire in transformer windings: enhanced electrical performance, increased durability, and improved reliability. It also offers best practices for selecting, handling, and applying copper wire in transformer construction. By following these practices, engineers and technicians can maximize transformer efficiency, enhancing overall reliability and effectiveness in electrical power systems.
Understanding Transformer Winding Copper Wire
Definition and Basic Properties of Transformer Winding Copper Wire
Transformer winding copper wire is a specialized type of wire used in the construction of transformer coils. It is characterized by its high electrical conductivity, excellent thermal conductivity, and superior mechanical strength. Copper wire is typically coated with an insulating layer to prevent short circuits and ensure safe and efficient operation. The wire’s flexibility and durability allow it to be wound tightly around the core of a transformer, creating the necessary magnetic field for energy transfer.
Comparison with Other Winding Materials Like Aluminum
While copper is the preferred material for transformer windings, aluminum is sometimes used as a cost-effective alternative. However, there are several critical differences between the two materials:
Conductivity: Copper has a higher electrical conductivity than aluminum, which means that it can carry more current for a given size. This makes copper more efficient, reducing energy losses and improving overall transformer performance.
Thermal Properties: Copper’s superior thermal conductivity allows for better heat dissipation, which is crucial in preventing overheating and maintaining transformer longevity. Aluminum, on the other hand, has lower thermal conductivity and can lead to higher operating temperatures.
Mechanical Strength: Copper is mechanically stronger than aluminum, which makes it more resistant to mechanical stresses and deformation. This strength is particularly important in applications where the winding wires are subject to vibration and other physical forces.
Durability: Copper’s resistance to oxidation and corrosion is better than that of aluminum, contributing to longer life and more reliable performance in harsh environments.
Weight and Cost: Aluminum is lighter and cheaper than copper, which can be advantageous in terms of cost savings and ease of handling. However, the trade-off is typically lower efficiency and shorter lifespan.
In summary, while aluminum winding wires can be used in some applications, copper winding wires are generally preferred for their superior conductivity, thermal management, mechanical strength, and overall reliability in transformer construction.
Benefits of Using Copper Wire for Transformer Windings
High Conductivity
Copper is renowned for its superior electrical conductivity, which is significantly higher than that of most other metals, including aluminum. This high conductivity allows copper to carry more current with less resistance, resulting in lower energy losses. When used in transformer windings, copper’s exceptional conductivity enhances the transformer’s overall efficiency, leading to improved performance and reduced operational costs.
Durability and Reliability
Copper is highly resistant to oxidation and corrosion, which are common issues that can degrade the performance of other metals over time. This resistance ensures that copper winding wires maintain their integrity and functionality in a variety of operating conditions, including harsh environments. The longevity and reliability of copper wires contribute to the extended service life of transformers, reducing the need for frequent replacements and maintenance.
Thermal Performance
One of the critical benefits of copper is its excellent thermal conductivity, which allows for better heat dissipation compared to other materials like aluminum. This superior heat dissipation is crucial for maintaining transformer performance, especially under high-load conditions where excessive heat can cause damage or reduce efficiency. Copper’s ability to effectively manage heat ensures that transformers operate safely and efficiently, even in demanding applications.
Mechanical Strength
Copper boasts impressive tensile strength and flexibility, making it an ideal material for transformer windings. Its mechanical strength ensures that the winding wires can withstand the physical stresses encountered during manufacturing and operation, including bending, twisting, and vibration. The flexibility of copper also facilitates easier handling and installation, enhancing the overall efficiency of the manufacturing process and simplifying maintenance tasks.
In conclusion, the use of copper wire for transformer winding offer numerous benefits, including high conductivity, durability, superior thermal performance, and mechanical strength. These advantages make copper the preferred choice for ensuring efficient, reliable, and long-lasting transformer performance.
Best Practices for Using Transformer Winding Copper Wire
Proper Sizing and Selection
Choosing the right wire gauge is crucial for the optimal performance of transformer windings. Proper sizing ensures that the wire can handle the required current without excessive heating or energy loss. When selecting the appropriate wire gauge, consider the specific application requirements, including the transformer’s voltage and current ratings, as well as the operating environment. Using charts and guidelines for wire sizing can help in making the right choice, ensuring both efficiency and safety.
Winding Techniques
To optimize winding efficiency, it’s important to employ proper winding techniques. Uniform winding helps to ensure that the magnetic field is evenly distributed, which is essential for the transformer’s performance. Avoiding overlaps and gaps in the winding reduces the risk of short circuits and improves thermal management. Techniques such as layer winding and segment winding can be used to achieve uniformity and enhance the overall quality of the windings.
Insulation and Cooling
Effective insulation is vital for preventing short circuits and ensuring the long-term reliability of transformer windings. Using high-quality insulating materials that are appropriate for the operating voltage and environmental conditions is essential. Additionally, incorporating effective cooling methods, such as oil or air cooling, helps to dissipate heat generated during operation. Proper cooling enhances the performance and lifespan of the transformer by maintaining safe operating temperatures.
Maintenance and Inspection
Regular maintenance routines are essential for ensuring the integrity and performance of transformer windings. Periodic inspections should include checking for signs of wear, corrosion, and thermal degradation. Ensuring that the insulation remains intact and effective is also critical. By following these maintenance practices, potential issues can be identified and addressed before they lead to significant failures, thereby extending the transformer’s service life and maintaining its efficiency.